Research project
Wood firing systems with up to 80% less NOx emissions
Together with project partner Endress Holzfeuerungsanlagen, Fraunhofer researchers have developed a new type of firing technology that can reduce NOx emissions by up to 80 percent. This means that future limit values can also be reliably complied with.
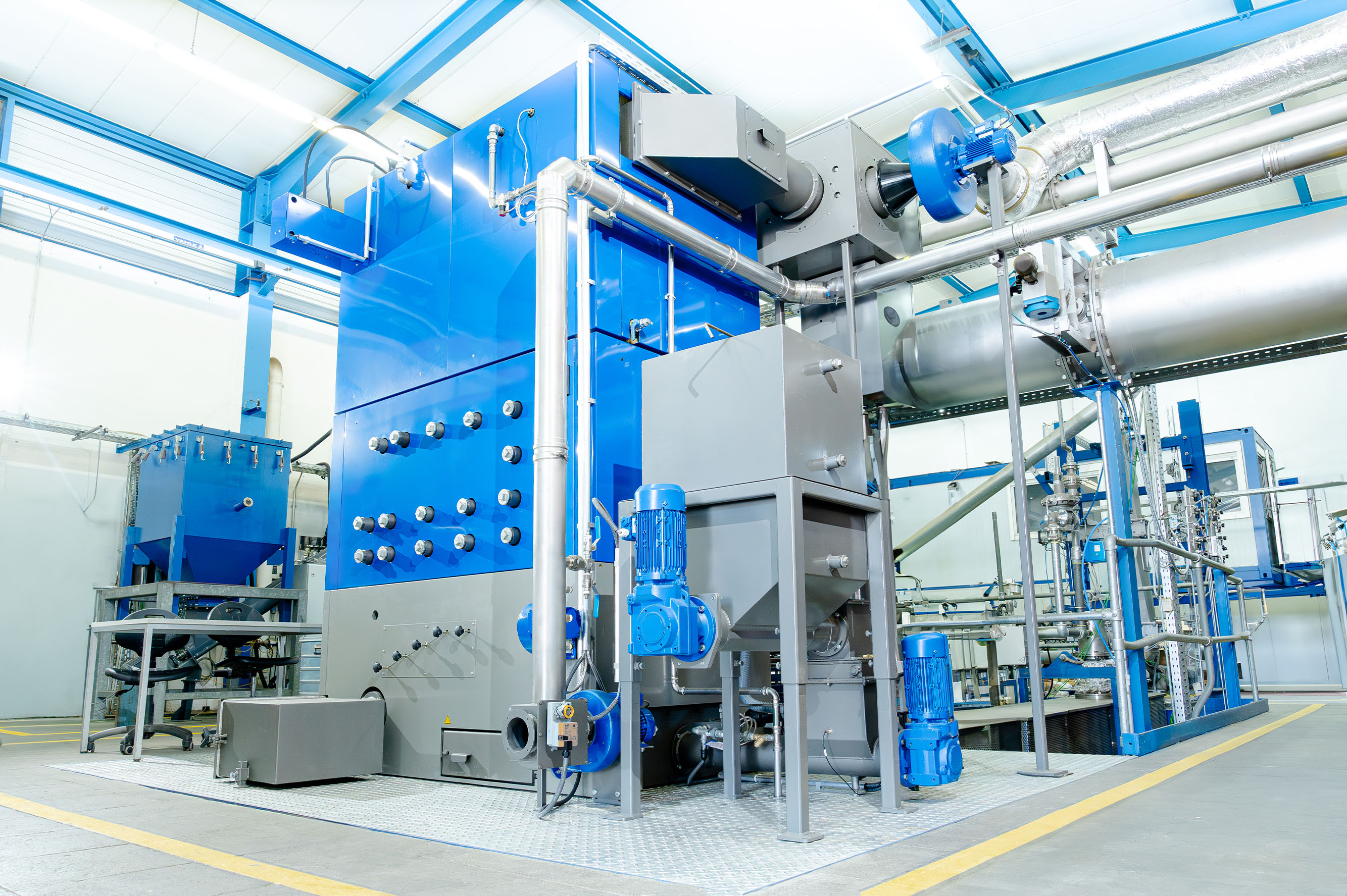

In a project funded by the German Federal Ministry for Economic Affairs and Climate Protection, the project consortium succeeded in demonstrating the principle of fuel staging in a medium-sized wood combustion plant. The goal of reducing nitrogen oxide emissions by at least 50 percent compared to the state of the art was exceeded: a reduction of up to 80 percent was demonstrated in the project.
The tests were carried out on an underfeed combustion system with a rated output of 250 kW. Briquettes made from chipboard residues with a high nitrogen content of 4.75 percent were used as fuel. Without reduction measures, the NOx emissions of the test system averaged 1,955 mg/m³N (based on a volume content of 6 percent oxygen in the flue gas). With fuel staging, the values could be reduced to an average of 361 mg/Nm³. A limit value of 370 mg/m³N oxide emissions at 6 vol.% O2, as prescribed in the German 44th BImSchV for medium-sized combustion plants, could thus be reliably undercut.
Markus Heese, Managing Director of Endress Holzfeuerungsanlagen, says of the results: »We were confident that the technology would also work for decentralized, smaller systems. The feasibility was demonstrated in advance by Fraunhofer. It is all the more pleasing that this has now been confirmed in the prototype and even exceeds the targets. We will definitely continue to pursue this approach.«
During the development, design and manufacture of the prototype, care was taken to ensure that existing systems could also be retrofitted in the future: in an industrialized form, the fuel staging system could be inserted as an intermediate module between the vault and the boiler.
Relevance for the wood processing industry
The technology's area of application focuses on medium-sized furnaces in the output range between 100 kW and 2 MW. To date, there is no adequate technical solution for nitrogen oxide reduction. However, such a solution would be particularly important for wood processing companies in order to be able to use painted, varnished or coated wood, chipboard, plywood or glued wood for energy in the future. Burning such wood is generally associated with high nitrogen oxide emissions. The discussions about NOx and particulate matter limits being exceeded also highlight the need for action.
There are currently no limit values for nitrogen oxide emissions in germany or the EU, which applies to small and medium-sized incineration plants. In the medium term, legislation is expected to be introduced. This would pose major challenges for manufacturers and operators of biomass furnaces.
Technology
The reduction in nitrogen oxide emissions in the new plant is achieved exclusively with the help of primary measures. Dr. Martin Meiller, Head of the Clean Combustion and Process Heat department at the Fraunhofer Institute UMSICHT, explains it this way: »In the primary zone, solid fuels such as wood residues or other biogenic fuels are burned conventionally. Another fuel, the reduction fuel, is introduced into the secondary zone. This creates a reduction zone in which nitrogen oxides are broken down with the help of hydrocarbon radicals.«
The secondary fuel used so far is natural gas, but other secondary fuels such as wood dust are to be tested at a later date in order to be able to completely dispense with fossil fuels. The research team and industrial partners now want to continue the project on the basis of the promising results and launch a market ready product in the coming years.
Last modified: